Understand how D-CBurner will bring advantages to your industrial process and reduce the emission of polluting gases
Dynamis has a series of equipment for the industry, such as hot gas generators, dryers, gasifiers and burners. Among the burners, the D-CBurner is the secondary burner developed by Dynamis for kiln precalciners.
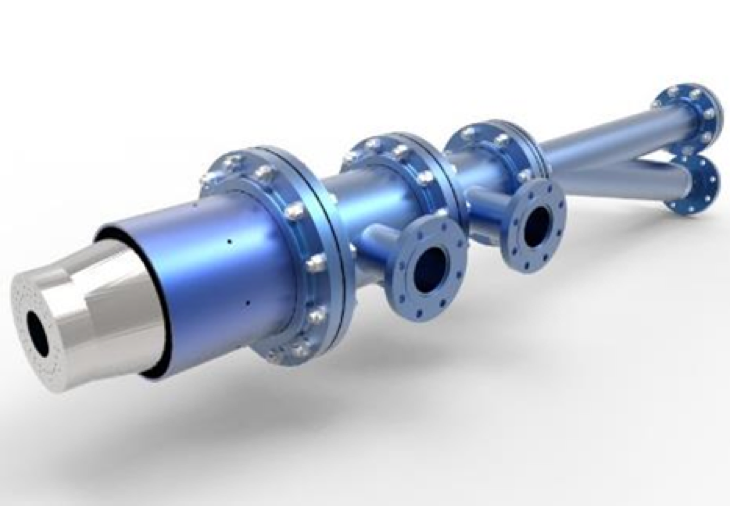
What are the advantages of D-CBurner?
D-CBurners can be installed in place of coal or petcoke injection tubes, for example, to improve the mixture of fuel and gases inside the precalciner through its two shaping air channels, the external one with axial component and the tangential one with axial and radial components, giving greater flexibility to the burner, allowing it to be adjusted to the needs of the process.
They are also often used to reduce NOx and CO emissions. In these cases, the entire burner design (shaping air injection nozzles, the number of burners used, their positioning in the precalciner, etc.) is achieved by means of computational simulations (Computational Fluid Dynamics Analysis – CFD), which allow to maximize the results and ensure that the foreseen objective (for example, of NOx reduction) is fully achieved.
Success case with D-CBurner
A successful case in the use of D-CBurners was their application in a cement plant in Egypt. The plant had an ILC-type precalciner between the smoke chamber and the lower cyclones, with coal being injected just above the tertiary air duct through 02 200mm tubes directly from the dosing system. The NOx emission at the tower output was about 750 to 800 ppm, with the customer’s intention being a 25% reduction in these emissions.
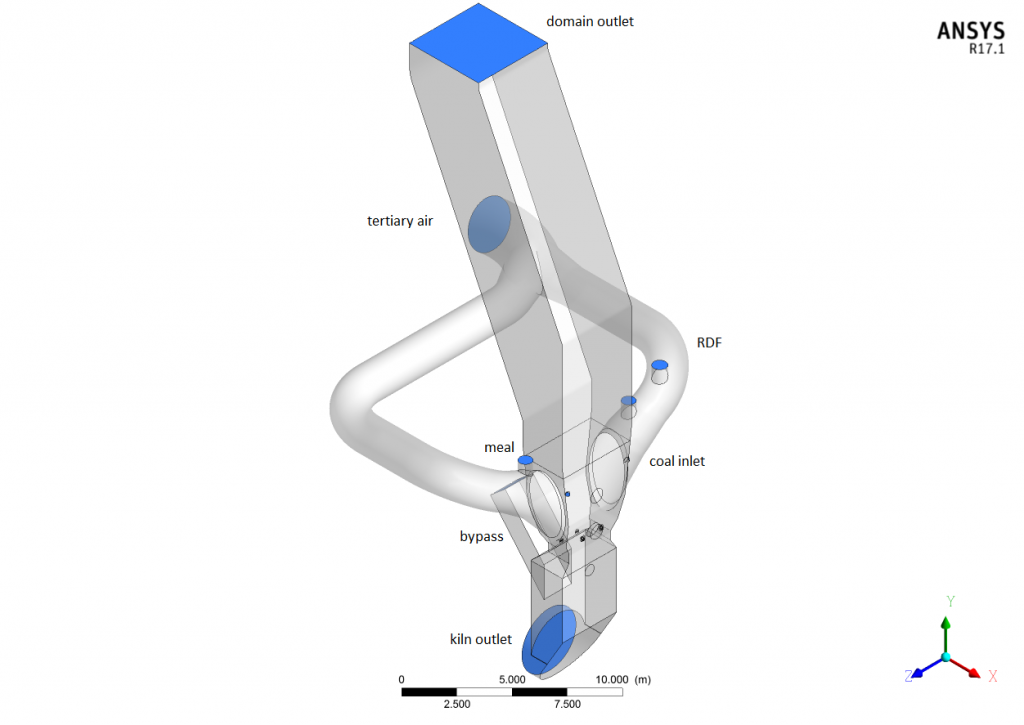
Through CFD simulations, the installation of 04 secondary burners at different points below the tertiary air duct was defined, with the results of the simulations pointing to a significant reduction in NOx emissions.
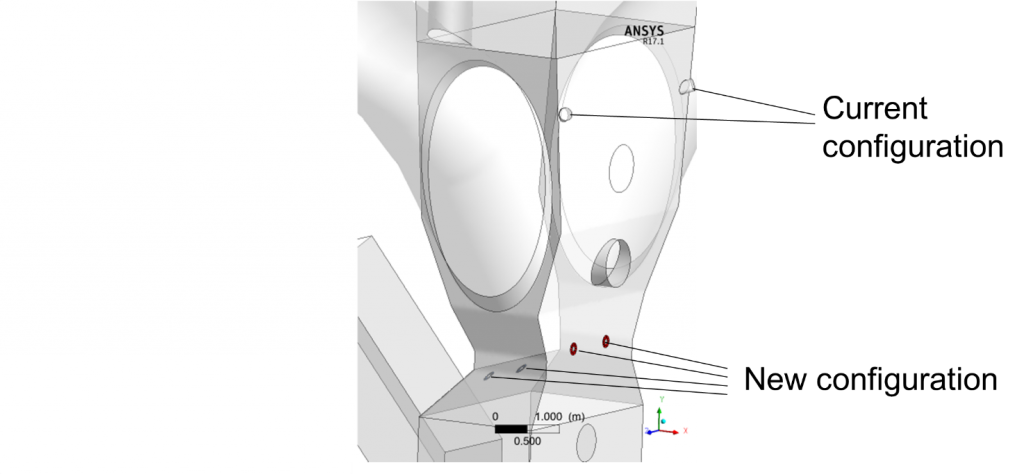
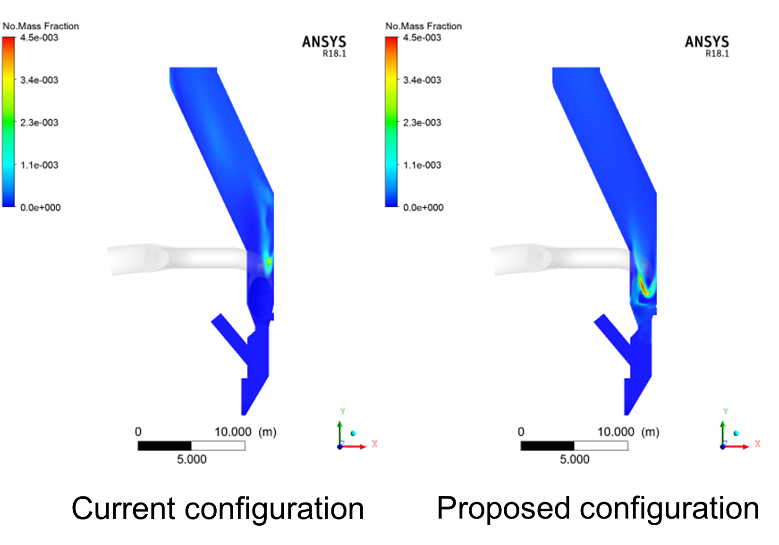
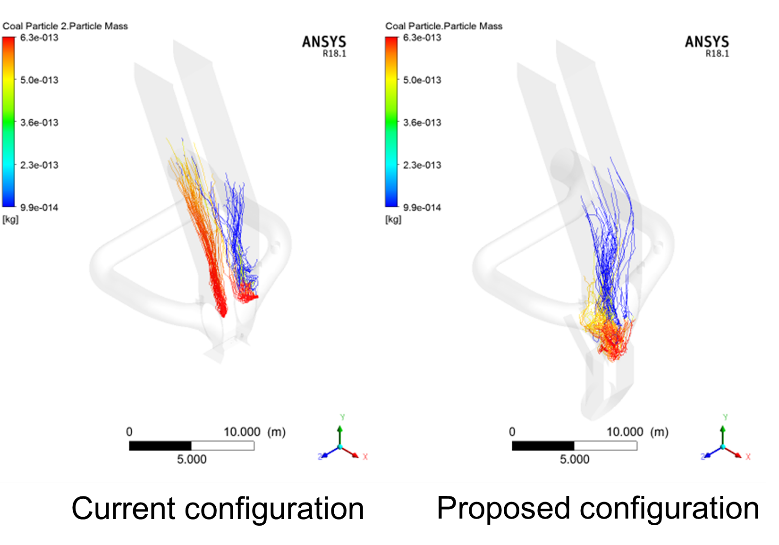
A set of 4 D-CBurners, their new shaping air fan, plus accessories such as butterfly valves and pressure gauges for air control was supplied. After startup, a 29.2% reduction in NOx emissions was observed, higher than the customer’s target of 25%.
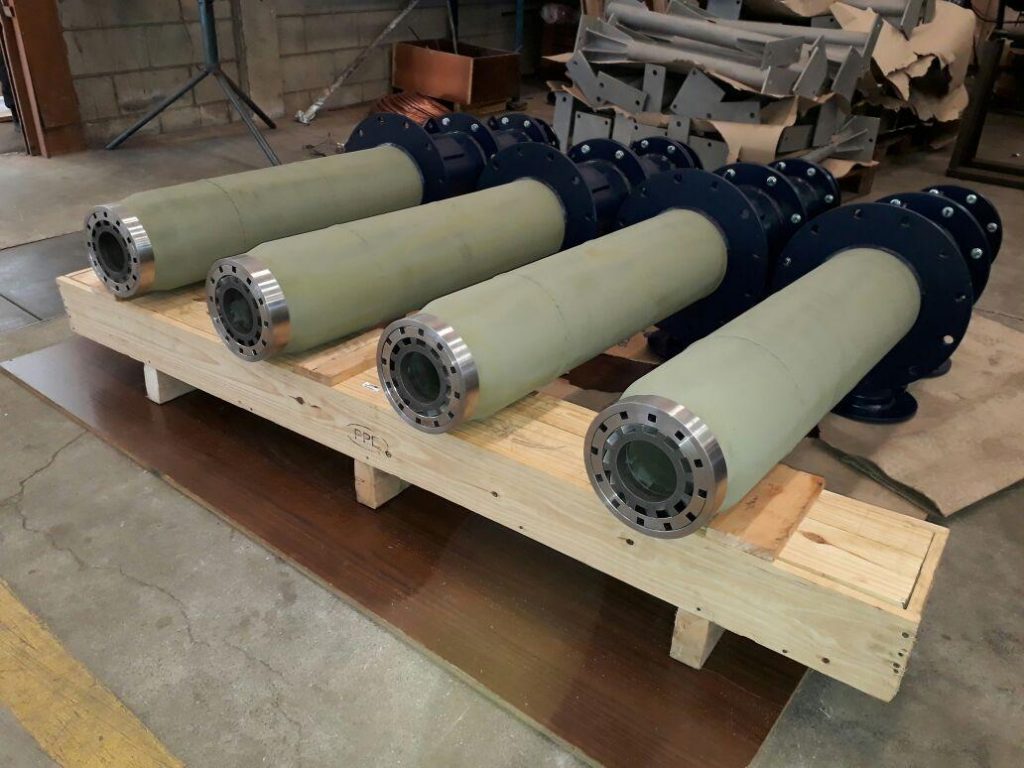
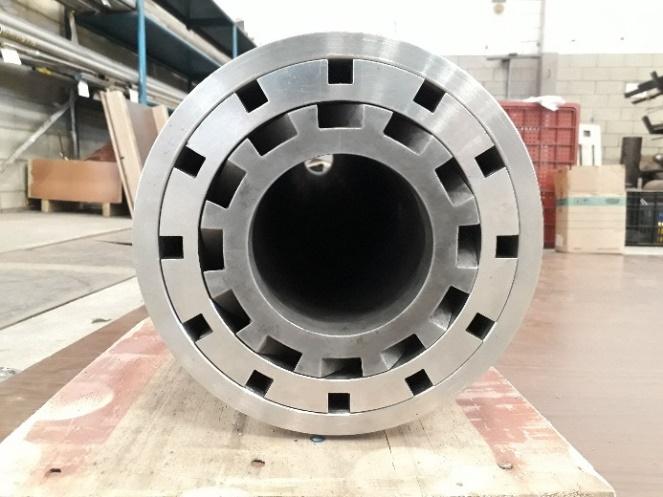
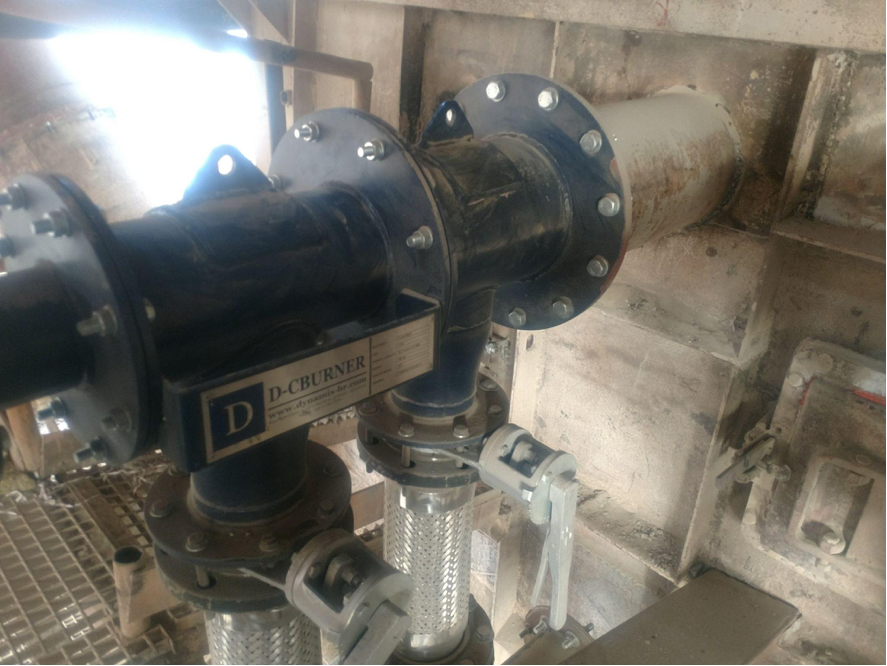
Dynamis has a range of equipment for different applications, developed by a technical body with extensive experience, using modern tools acquired in the market and some even developed internally. Evaluating existing systems, identifying bottlenecks, studying improvements, and supplying equipment, Dynamis works at all stages of the project to ensure that your company will have the best solution for your process. For Dynamis, trust matters.
Team Dynamis