Rotary kilns are systems with a wide range of applications. They are used for many types of thermal processing, being responsible for chemical reactions and physical changes in materials.
As many applications of rotary kilns are similar in terms of temperatures, pressures and flows, it is possible that the same kiln can be used for the production of different materials. For this reason, there are several cases of cement kilns that have been modified to be used on a new mission, such as lime production, ores calcining or calcined clay production.
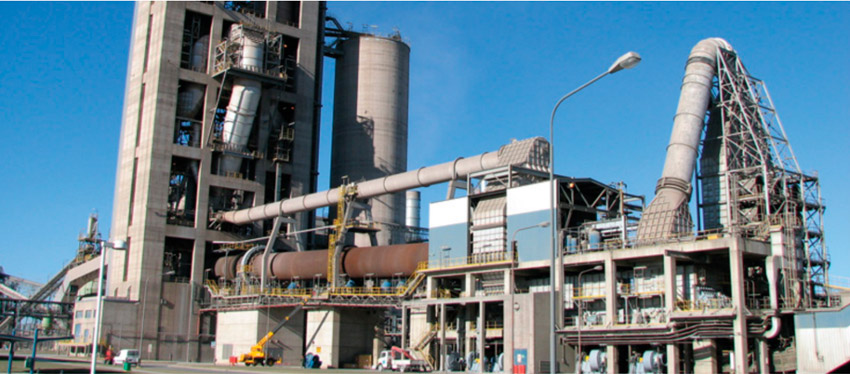
There are numerous examples of modified cement kilns in the industry, but only a few with easily reversible modifications or that fit to a wide range of processes. This leads us to some questions: Nowadays, why use single product processing kilns? Why not produce different products according to market demands? Why not use the periods when clinker silos are full for drying cement mill additives such as slag, gypsum and clay?
We know that there are several reasons why most clinker kilns produce only this material, such as operational efficiency and modification costs, but we are convinced that it is possible to reach the production flexibility that today’s market requests with low costs and high efficiency, through multitask kilns.
Applications for multitask kilns
FLEXIBILITY: this is the biggest advantage of a multitask kiln. By having several different applications with few reversible changes in configurations or equipment, a multitask kiln can adapt its production to a specific period of the year, or to a market opportunity. In a scenario of low cement demand, such as the one we are experiencing, your clinker kiln could be used, for example, to:
- Dry slag
- Dry gypsum
- Dry bottom ash
- Dry clay
- Produce calcined clay
- Produce lime
- Produce agricultural lime
- Calcine ores in general
Several of these additives are introduced wet in cement mills and are dried using electrical energy!! That is, they are dried at a very high cost!!
How to turn your kiln into a multitask one?
Obviously not all materials can be dried, calcined or processed in a particular clinker kiln, as the flexibility of a kiln is limited by minimum and maximum allowed values of air and fuel flows and material temperatures and grain size, among other factors.
Thus, it is necessary to carry out an initial study to verify the characteristics of line’s main equipment, obtain current operating parameters and determine the future ones and, finally, identify the main bottlenecks and limitations for using the clinker kiln in another process. Usually, the main limitations for kiln flexibility are:
- Material Feeding and Dosing System
- Cooling system
- Exhaust system
- Combustion system
Dynamis, with its technical team of multidisciplinary and highly experienced engineers in various industry segments, can assist you from an initial technical-financial feasibility study to the mechanical and electrical detailing of the solution, in addition to supplying all necessary equipment for kiln flexibilization. All these activities are carried out within deadlines that meet the fast market changes, always allowing a quick return to clinker production when necessary.
Dynamis solutions for multitask clinker kilns
Not sure what to do with your low load operating cement kiln?
Worried about a low cement consumption market?
Want to serve new segments and new customers?
Want to gain productivity and flexibility in your cement kiln with new products?
Want to optimize your energy consumption?
Need innovative solutions in a highly competitive and challenging market?
Contact us through our website and make an appointment for a new tailored process to your cement kiln!
Dynamis team