Over the years, companies have been searching for business models that can bind both development and sustainability. New environmental regulations and commitments to society have put pressure on companies to lower their carbon footprint, and minimise the use of fossil fuels and electric power. On the other hand, in a more global and competitive world, markets force companies to lower their prices and cut production costs in order to stay viable.
In the cement industry, one solution is to produce artificial pozzolan to be used as an additive in cement production as a substitution for clinker.
Pozzolan
Pozzolan can be classified in two types: natural pozzolan is found around volcanoes (sometimes called pozzolana) and artificial pozzolan is a material created through the use of a kiln (occasionally named natural calcined pozzolan).
Many cement producers are aware of pozzolanic- like materials, such as metakaolin, flyash and blastfurnace slag, but an increasing number of plants are investing in the calcination and activation of clays as a means to boost the usage of pozzolans in cement production.
The chemical composition of pozzolanic clays can vary in each region, but generally the silica (SiO2) content is around 55 – 70% and alumina (Al2O3) content is between 15 and 30%. The important point in this matter is to ensure the maximum silica content and, consequently, the most reactive with calcium hydroxide. The result of that reaction is a calcium silicate compound with strengths that may vary from a small percentage to almost the same as ordinary Portland cement.
Advantages of using pozzolans
There are four main advantages in using pozzolans, as outlined below.
Increase in production
One of the main advantages of using pozzolan is the increase in cement production compared to equivalent amounts of clinker, given that some cement types can contain up to 40% pozzolanic material (according to ASTM C 595). In some countries, this figure can reach 50%.
Lower investment requirement
Compared to a clinker line, a pozzolan line costs 60% less, consists of less equipment and requires fewer personnel (operation and maintenance) for operation.
Lower thermal and electric power consumption
As there is no need for a raw mill (the pozzolan clay only needs to have its lump size reduced to be fed directly into the kiln) and the material requires no clinkerisation, it only needs to be dried, heated to 900 ˚C (between 700 and 900 ˚C, depending on the clay) and activated (to have its porosity increased to enhance the surface area and reactivity). The fuel consumption of a pozzolan clay activation line is significantly lower than a clinker line.
Fewer CO2 emissions
The production of 1 kg of clinker typically leads to 0.85 kg of CO2 being emitted (0.54 kg emitted as a result of limestone decomposition: 0.31 kg from flue gas). Pozzolanic clay activation does not take place in thermal decomposition of carbonates, which is highly positive in this aspect.
Additionally, as the cement with pozzolan material requires less energy (both thermal and electric) to be produced, the amount of CO2 generated is considerably lower.
Pozzolan line
Dynamis was asked to develop a pozzolan calcining line to burn 100% pulverised petcoke. The fuel was available in the client’s plant, and only light fuel oil should be used to heat up a system (Figures 1a/1b).
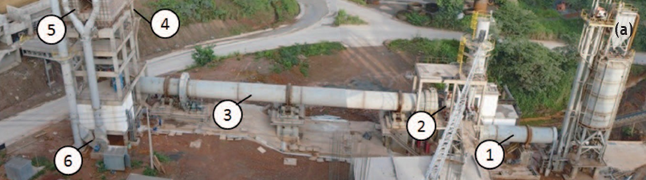
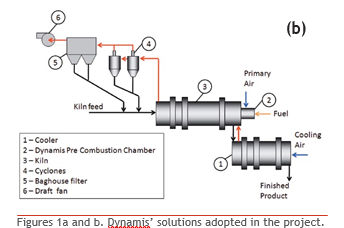
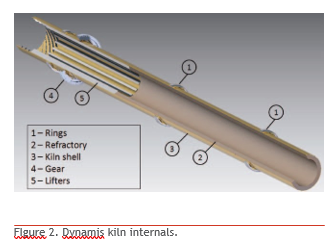
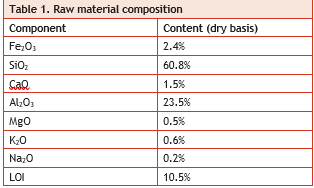

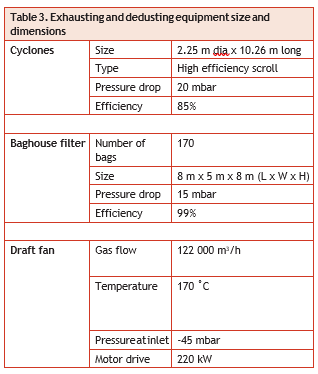
Challenges
When burning pulverised solids, some conditions must be observed to ensure a stable combustion, often called the three ‘T’s of combustion:
- Temperature.
- Time.
- Turbulence.
On clinker kilns, the conditions are suitable to burn all sorts of fuels (including pulverised solids).
On the pozzolan line designed by Dynamis, the clay used as raw material required that the final product had a target of 1.5% LOI (loss on ignition). If the material was fully calcined, part of it could be sintered and its cement properties lost. Therefore the process temperature is significantly lower (up to 900 ˚C), so even with sufficient turbulence there could be occasions when the basic conditions to burn solid fuels were not met, causing operational upset conditions (i.e. flame extinction, or temperatures too high to maintain kiln operation).
One other condition that is particularly difficult to stabilise is the amount of dust in the kiln. On clinker lines, even with dusty kilns, the temperature and turbulence factors help to keep combustion steady.
The current technology used to produce activated clay as pozzolan has its origins in clinker kilns and, on top of that, most of the systems implemented today are based on kilns equipped with satellite coolers.
On pozzolan lines, where temperatures are lower, there are kilns that have up to four stops a week, due to flame extinction alone, and each kiln restart – besides the loss in production – requires auxiliary fuel to heat the system before feeding, thus increasing the operational costs. The raw material composition is illustrated in Table 1. The clay, as received, had average moisture of 20% (wet basis) and, together with the fact that the LOI of the material was mainly due to bound water, the kiln itself would work both as a dryer and a calciner. With experience using both systems, Dynamis has implemented specially designed lifters, so the heat and mass exchange would be increased at the gas outlet of the kiln, effectively enabling the use of a shorter kiln. Dynamis took advantage of the fact that the moisture of the material during the drying stage can hold down the temperatures on the kiln shell (as in a dryer), meaning that less refractory bricks would be required.
A rotary cooler was chosen for this application, since the secondary (cooling) air was enough to refrigerate the product and no additional air was needed. A grate cooler is more efficient, but since the material outlet temperature is already low (approximately 120 ˚C), and taking into account the additional cost and equipment complexity of a grate cooler, this option was not economically attractive.
The cooler also has a small portion of refractory material (to receive the hot material from the kiln) and lifters to enhance thermal exchange with cooling air (which is heated and used as secondary air on the kiln).
Combustion
To allow proper conditions for burning petcoke, in order to maximise the use of preheated air (from the cooler) and to separate the dust factor from the combustion process, Dynamis developed a precombustion chamber that allows the combustion of petcoke to be initiated inside the chamber and to finish inside the kiln hood (Figure 3).
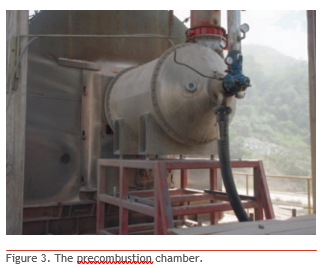
The precombustion chamber uses 100% petcoke (up to 2000 kg/h) and operates at sub-stoichiometric conditions. Thus the precombustion chamber acts like a gasifier, transforming the solid petcoke particles into a flue gas with a high amount of CO.
The outlet temperature is estimated (through the use of CFD) to be around 1300 ˚C, and CO content is approximately 13%.
The high CO content at the chamber outlet could mislead one to assume that, at the kiln outlet, a huge amount of carbon monoxide is discharged to the atmosphere. But the combination of high gas temperature at the chamber outlet and hot secondary air allows the full combustion of the remaining gas to take place on the kiln hood, and CO content at the kiln outlet is less than 100 ppm (at 10% O2).
Another potential use for this technology is to activate pozzolan clay with high amounts of iron oxide (Fe2O3), a compound that may give a pink aspect to the cement. This type of clay needs to be processed in a chemical reducing atmosphere, which provides conditions for FeO formation and very small colour deviation in the final product.
Exhaust and dedusting system
On the kiln outlet, a pair of high efficiency cyclones captures most of the dust from the flue gases. A baghouse filter completes the job by removing any additional material to less than 50 mg/Nm3 (according to regional regulation). Special attention has been paid in the selection of construction materials, given that the flue gas temperature could fall below acid dew point in some parts of the system, leading to corrosion and premature material failure.
The system was designed without any flue gas scrubber, given that the petcoke used had low sulfur content. If the fuel has high sulfur content, a more complex gas cleaning system must be installed, mainly because the process does not absorb the SO2 as a clinker line does.
Comparison of Dynamis system and typical satellite kiln
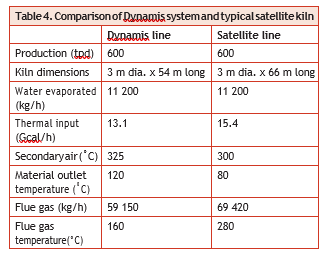
A comparison of the two alternatives is shown in Table 4.
When analysing these figures, it is important to notice that both kilns produce the same amount of activated clay; the thermal input on a satellite kiln is almost 18% higher.
Comparing the energy output, it is possible to determine why the Dynamis line is more efficient: the flue gas temperature and mass flow are significantly lower than on a satellite cooler line (although the product discharge temperature is higher).
With the available energy input (fuel flow), the Dynamis line uses 58% to remove bound and surface water. On a satellite kiln, only roughly 48% is used for this purpose.
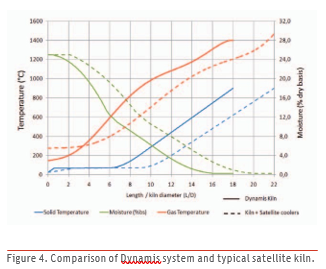
Figure 4 illustrates differences between the two alternatives. The Dynamis line can be shorter (lower L/D ratio), and the flue gas temperature is considerably lower.
Dynamis is searching for new ways to increase the thermal efficiency and believes there is still room for improvements. But one key goal has been reached: some longstanding preconceptions about rotary kilns have been altered with positive results.
Dynamis Team