Grinding and drying fuel in your industrial process can positively impact your company’s finances. Understand!
The objective of the entire industrial sector, regardless of the size of the company, is to obtain high performance with its processes, great cost-benefit with its operations and, of course, generate profits for the business.
However, depending on the sector in which it operates, profits may be slightly lower due to the high cost in several stages of industrial processes. Knowing this, many companies pursued ways to reduce costs with their operations, especially with fuel to combustion energy, which are one of the biggest costs in the industry.
With of the high price of fuels, a great way they found to reduce it was to use alternative fuels such as mineral coal, charcoal, among others.
For this, grinding and drying units for such products have been installed in some industries, but what is the real financial impact of grinding and drying fuel on the industrial process? Understand in today’s post from Dynamis.
What is fuel grinding and drying and why does it have a financial impact on the industrial process?
The grinding and drying of solid fuel are process to and make the grain smaller to be used in manufacturing operations in industries such as cement, cellulose, among many others, to further improve its combustion.
Being commonly used in fuels, such as mineral coal, charcoal, among others, the use of a mill to grind and dry them can help the industry to have a cost reduction with the whole process, since the use of these types of fuel in the calciner or main burner is also one of the best ways to reduce kiln costs.
This type of grind can be done with two types of mills.
Mill for grinding and drying fuel
Ball Mill
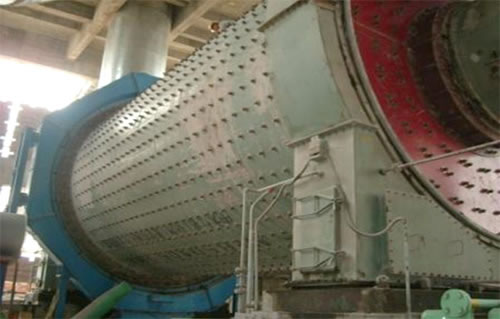
Being widely used for the coal grinding operation, ball mills have strong ventilation and all ground products are transported to the separator equipment a cyclone or a screen.
Due to their process characteristics and simple mechanism systems, they have proven to be quite satisfactory, especially in the grinding of abrasive coals and with a high ash content. In addition, one of its biggest advantages is the great resistance to abrasion, together with the low cost advantage for the replacement of parts, when necessary.
In the mill, the material normally passes through a drying chamber that is protected by coating plates, made of high chrome cast steel, which are resistant to wear and lifting elements in carbon steel.
The first row of them transports the material to the interior, so that it keeps the entrance unobstructed while the others will promote the flow of wet and new materials into the hot air stream.
Vertical Roller Mill
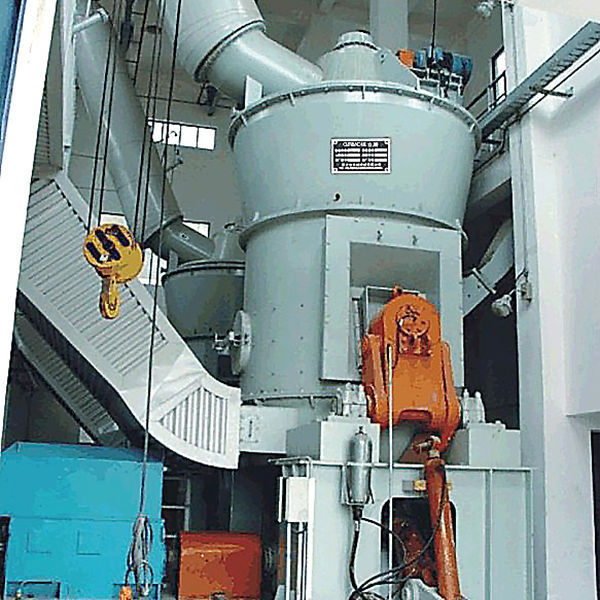
Vertical roller mills have a cylindrical housing with a dome-shaped upper section to protect against some effects of explosions, in addition to internal surfaces that are not horizontal to prevent the disposal of coal dust and spontaneous ignition.
The beginning of the grinding and drying of the fuel, like coal, for example, occurs on a rotating table and some grinding rolls, which can be 2, 3, 4, etc … The current principle is similar, with the fuel new fed into the center of the table and it will pass through the space that exists between the rollers and the table, how long it will be hydraulically, with the ground material being carried by the hot air stream.
Developing a fuel grinding and drying project in the industry can be a high investment, but the cost drop with the use of alternative fuels will bring a great financial impact to your industry, making the project to install this equipment for grinding a great cost-benefit!
Dynamis Team