Since its first Alternative Fuel Combustion System project in 2004, Dynamis has performed over 50 projects involving the use of alternative fuels. All of them operated with different types of fuel in plants of the most important cement companies. This experience made it possible for Dynamis to define the minimum characteristics to be met by alternative fuels and injection systems, so that it is highly robust and highly reliable (and thus can reach substitution levels above 70% without compromising the operation or clinker quality), yet still maintaining a certain simplicity in its concept and installation.On the foundation of all this technology is the use of simulations in CFD software. With this, Dynamis has developed a method to define optimum quantity and the best injection points for fuel injection, either in the calciner or in the riser duct. This process takes into account several operating parameters (temperatures, oxygen concentrations, gas velocities), the calciner geometry (and of the smoke box / riser duct) and fuel properties.
Dynamis has technical competence and personnel capacity to work with a scope that goes from fuel transportation (waste shed) to its combustion inside the calciner, encompassing all the disciplines involved: processes, mechanics, electrical, civil, instrumentation and automation.
The D-Flame burner has been developed aiming improvement in combustion efficiency for both main and alternative fuels.
One of the successful cases of solid fuel are the kilns at the Degerhamm plant in Sweden. With the use of the D-Flame burner, a thermal substitution of approximately 70% occurs using RDF and other organic wastes.
Other successful case is the burner of the kiln in one of the plants in Cantagalo/RJ. After the installation of a lance supplied by Dynamis to inject liquid waste, there was an increase of approximately 70% in the volume of oil waste injected.
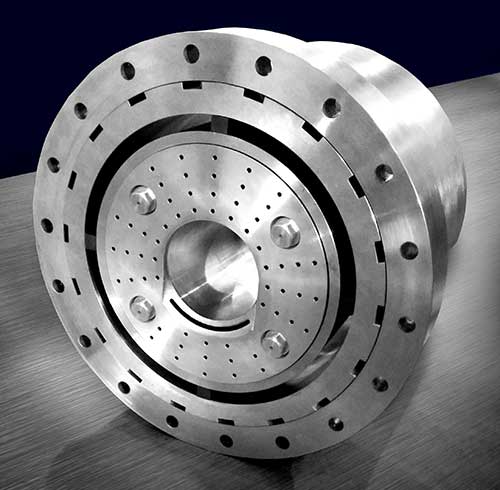
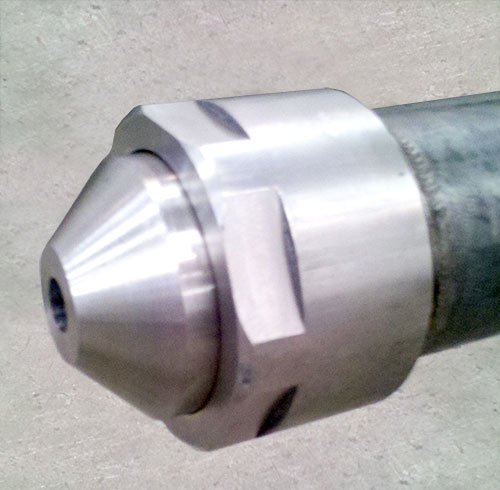
The use of fuels with high Sulphur content, specially petcoke with high Sulphur content, are an option for cost reduction compared with mineral coal, oils and even compared with the petcoke with low Sulphur content.
High levels of Sulphur in fuel are related to higher recirculation of fines. Usually this amount of powder compromises the kiln stability and consequently the size and shape of clinker crystals.
The optimized burner tip geometry and the operational parameters associated with the primary air, specially flows, pressures and injection velocities in D-Flame burners offset the negative effects of Sulphur in the kiln. This is proven by the installation of the D-Flame in the W8 kiln of Votorantim Cimentos plant in Rio Branco do Sul/PR – Brazil. Even operating with high Sulphur petcoke (5 to 6% Sulphur), the kiln stabilized faster than usual, and produced clinker crystals 14% smaller compared to the kiln results with the previous burner.
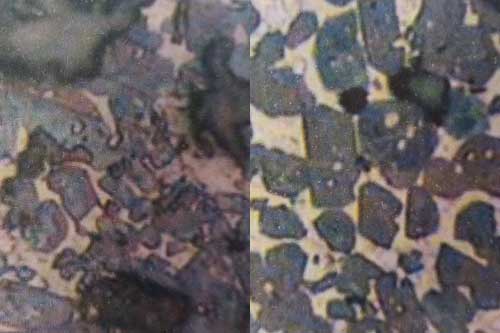
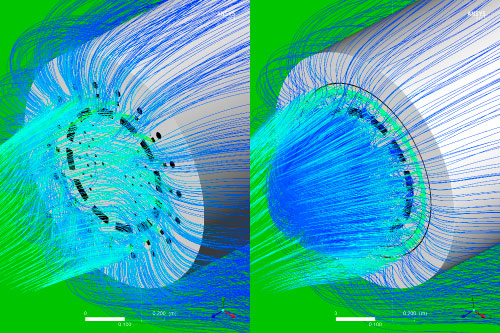
The use of pulverized solid fuel as a substitute for oil or gas in hot gas generators can significantly reduce operational costs for grinding and drying. Generally, this fuel replacement entails a high implementation cost due to the need for large-sized equipment and/or significant changes in layout.
The D-Gasifier is a compact gasifier, which can be installed in an already existing hot gas chamber, replacing the conventional oil or gas burner, and it requires minimal layout modifications.
In a cement mill from a plant located in Ceará, Dynamis replaced a conventional natural gas burner with a D-Gasifier. Since this equipment, with a power of 6 Gcal/h, gasifies the fuel with a very high efficiency, the cement plant had a cost-saving equivalent to the direct fuel price difference (R$/cal). The return on investment was only 6 months.
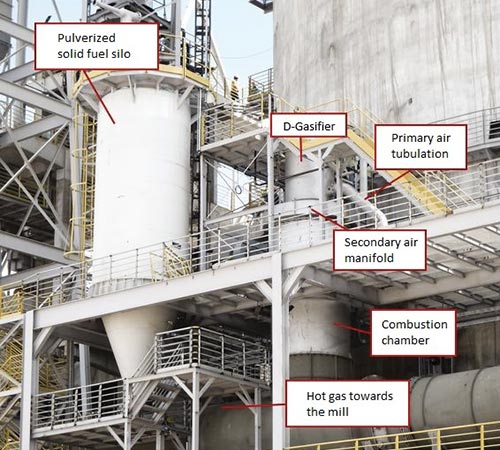
The use of biomass or combustível sólido bruto replacing oil or gas in hot gas generators can bring a significant reduction in operational costs for grinding and drying. Generally, this fuel replacement entails a high implementation cost due to the need for large-sized equipment and/or significant changes in layout.
The Fluidized Bed Hot Gas Generator by Dynamis was developed through research in partnership with research Institutes and Universities. Using the software CeSFaMB™/ CSFMB©, which simulates fluidized beds, and the knowledge from previous fluidized bed projects implemented by the company with various types of fuel, Dynamis developed the most compact and optimized solution for hot gas generation. Both crude fossil fuels (coal and petcoke) and different biomasses are used. Among them: acai lump, charcoal, wood chip, sugar cane, elephant grass and rice husk.
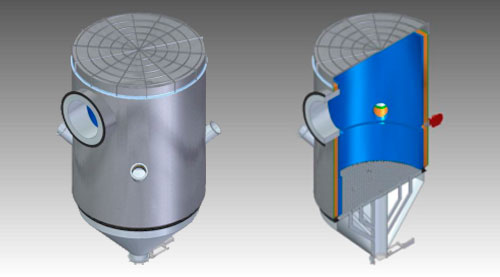
There are several sources of residual heat in cement, lime and pozzolan plants. Among them are exhaust gases, hot air and hot liquids from chillers, and waste gas from kiln. This waste heat can be used for the generation of electricity, through a Waste Heat Recovery system, which reuses this thermal energy to generate steam that drives the turbines, in a process called cogeneration.
Dynamis has already carried out several studies in the field of residual thermal energy recovery from cement kilns for the generation of electricity. To evaluate the technical-economic feasibility of the project, Dynamis comes up with a few cogeneration alternatives. The competitiveness between them is analyzed by comparing budgets and assembly costs at the local level. Finally, the results of this elaborated analysis results in recommendations to be presented to the client. Dynamis can also evaluate other aspects that can affect the project, such as safety, environmental issues and the electrical integration of the cogeneration unit with the daily operation of the plant.
The optimized geometry of the D-Flame burner tip and the operational parameters related with primary air, specially flows, pressures and injection velocities significantly improve the mixture of secondary air and fuel, resulting in a more stable flame.
The successful case of the D-Flame installation in the W8 kiln of the Votorantim Cimentos plant in the city of Rio Branco do Sul / PR, Brazil, has proved the impact of improved mixture of fuel with secondary air on clinker quality. With the new D-Flame burner, the kiln started to produce a clinker with 14% smaller C3S crystals (from 23.35 μm to 20.33 μm). As a direct result, a reduction of the same order in electricity consumption for the mill was obtained.
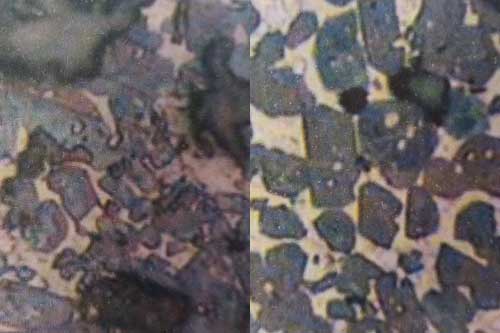
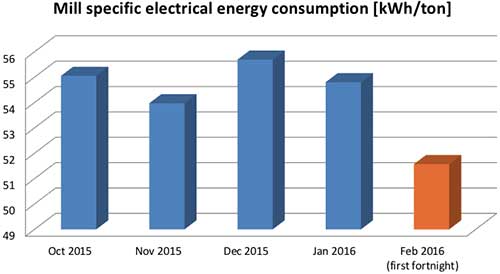
The high cost of electricity may be related to equipment inefficiency for not operating at its highest energy potential, which impairs productivity.
Through a detailed study of energy efficiency, it is possible to reduce the consumption of electricity. This study aims the identification of operational conditions that undermine the system efficiency. Dynamis team, by means of its extensive experience in the thermal, energy and fluid fields, identifies processes that can be optimized and proposes alternatives for an increase in the kiln’s energy efficiency, to meet the client’s need, respecting the operational limitations of the system.
In many countries, pozzolan can replace clinker in cement composition at rates of more than 50% (natural and/or industrial). Pozzolan cements offer advantages over ultimate strength and corrosion, as well as drastic reduction in CO2 emissions. In general, they have a lower specific energy consumption than clinker, both thermal consumption (about 25% less than clinker) and electric (about 15% less than clinker).
Dynamis has developed several projects related to Pozzolan. Among them, there is a plant located in Colombia. In this case, Dynamis developed a process for drying and activation (production of industrial pozzolan), as well as for changing clay color from red to gray, enabling the maintenance of cement’s characteristic color when mixed.
In this project, Dynamis developed the entire engineering project, reusing the old kiln for the production of clinker, and other existing equipment from two other clinker plants owned by the client. Dynamis also optimized the integration of this equipment, significantly reducing the cost and time for the project implementation.
Dynamis’ pozzolan production process, whether it involves color changing or not, undergoes drying by use of D-FDryer and D-HotGas. In a rotary kiln, the calcination is carried out in a controlled atmosphere. The key to this process is the use of D-Gasifier as the kiln’s main burner. This is an innovative production process in which a great deal of research and development has been employed for definitions such as the ideal blend of clay from different mine locations, process parameters, ideal pozzolan blaine, among other process and product variables. To verify the results, IPT (Institutes of Technological Research) was hired to prove the analysis of clay characterization and to carry out tests to confirm practical results of cement characteristics with the use of modified pozzolan.
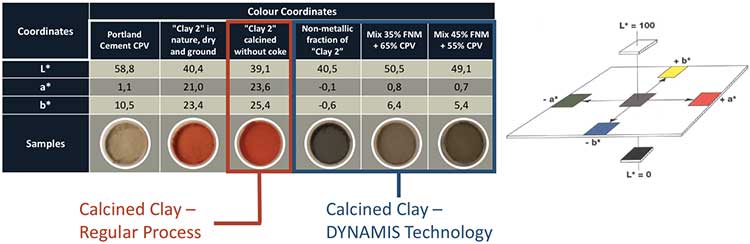
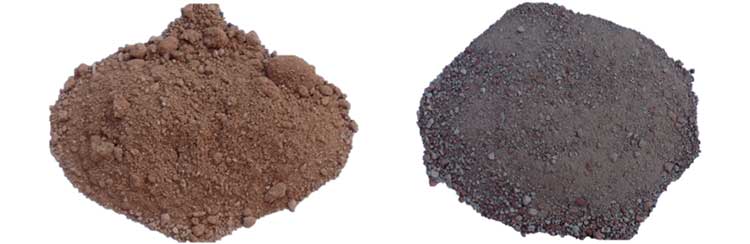
One of the major industry problems is Nitrogen Oxides (NOx) emissions, controlled by environmental agencies. These gases form due to the high temperatures of thermal processes, and many companies cannot control their emissions. Therefore, they are forced to inject gases to reduce NOx, significantly affecting their operational costs.
Dynamis offers a customized and complete solution for the reduction of NOx emissions. Consequently, it has an impact on cost reduction resulted from NOx reduction. This solution starts with a data collection at the customer’s plant and a simulation of the current operational condition. After the simulation, an engineering study involving methods and tools for kiln evaluation is carried out. In this study, computational fluid dynamics simulations are used in the application of complex models to simulate chemical kinetics and turbulence in industrial combustion processes. Thus, it is possible to define which equipment and processes will have the most effect in reducing nitrogen oxides emissions. By the end of the study, Dynamis is able to predict with reasonable precision the possible NOx reduction after implementing the modifications recommended.
Among the success cases is that of a clinker production line in Egypt. After the engineering study, the fuel injection positioning and some other parameters were modified. Together with the use of the D-CBurners burners, it was possible to obtain a better gas-fuel mixture. Initially, a 25% reduction in NOx levels was estimated.
Due to the rapid return on investments of the proposed modifications, Dynamis was hired to implement the project and to supply the D-CBurners. After the commissioning of the burners, almost 30% reduction in NOx emissions was recorded.
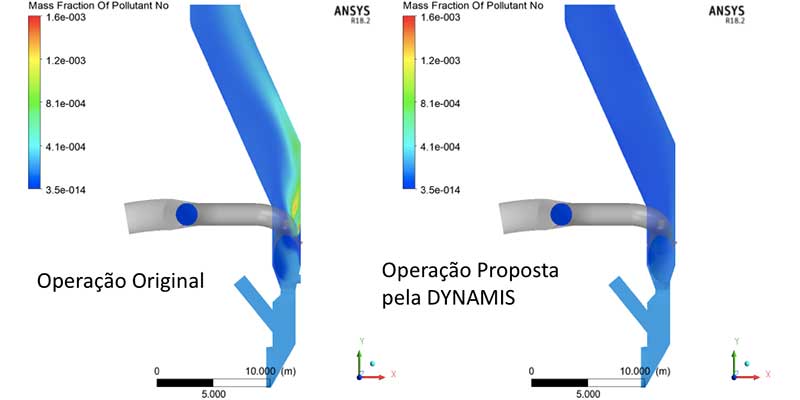
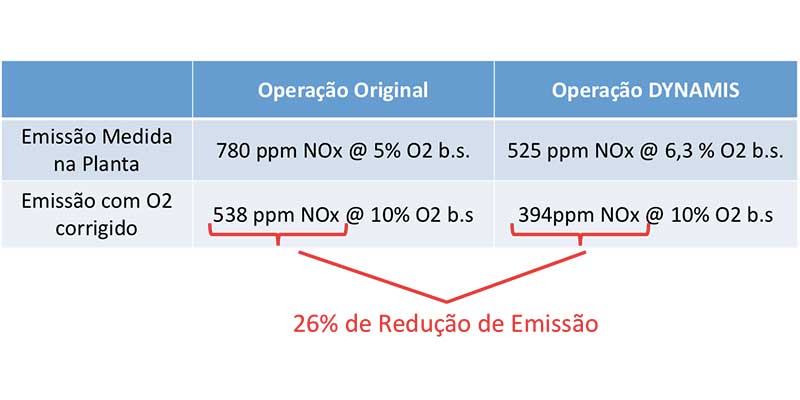
Cement kilns operation requires combustion air above stoichiometric index, but excess air alone does not guarantee a low CO emission. High emission rates of this pollutant result from incomplete combustion caused by insufficient mixing of secondary air with fuel. D-Flame optimized burner tip geometry and primary air operational parameters, particularly flows, pressures and injection speeds, significantly improve mixture of secondary air with fuel, resulting in good combustion, with low CO emissions.
Incomplete combustion can occur specially in burners operated with solid waste, when part of the injected residue falls into the kiln without burning. In such cases, Dynamis technology enables a more horizontal injection of solid waste, so that the residue remains in contact with the flame, increasing its combustion. Dynamis has already developed several successful cases of solid waste injection optimization, which enabled a better combustion, and, consequently, lower CO generation. As a direct result, it is even possible to increase the consumption of solid waste, which is often limited by high CO emission rates.
The most predominant reaction in the clinker process is calcination, so that approximately 35% by mass of kiln feed becomes CO2. For this reason, the most efficient solution to reduce its emissions in cement production is the replacement of clinker with other materials, such as pozzolan, fly ash or steel slag, which can reach up to 70% replacement. Slag and fly ash are byproducts of other processes, so they have a low added value and, like pozzolan, can contribute to the cement cost reduction.
In many countries, pozzolan can replace clinker in cement composition at rates of more than 50% (natural and/or industrial). Pozzolan cements offer advantages over ultimate strength and corrosion, as well as a drastic reduction in CO2 emissions.
Dynamis has developed several projects related to Pozzolan. Among them, there is a plant located in Colombia. In this case, Dynamis developed a process for drying and activation (production of industrial pozzolan), as well as for changing clay color from red to gray, enabling the maintenance of cement’s characteristic color when mixed.
The optimized geometry of the D-Flame burner tip and the operational parameters related with primary air, specially flows, pressures and injection velocities significantly improve the mixture of secondary air and fuel, resulting in a more stable flame.
The successful case of the D-Flame installation in the W8 kiln of the Votorantim Cimentos plant in the city of Rio Branco do Sul / PR, Brazil, has proved the impact of improved mixture of fuel with secondary air on clinker quality. With the new D-Flame burner, the kiln started to produce a clinker with 14% smaller C3S crystals (from 23.35 μm to 20.33 μm). As a direct result, a reduction of the same order in electricity consumption for the mill was obtained.
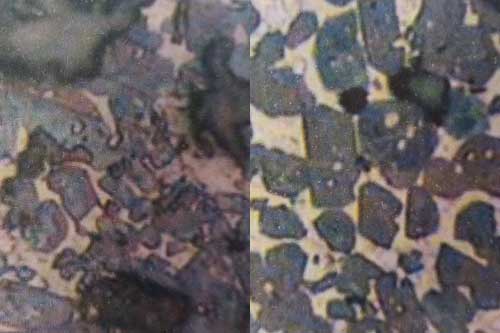
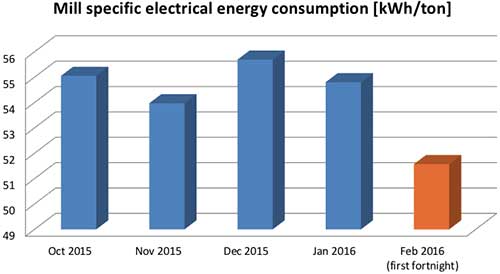
Whatever causes flow increase without consequently improving productivity can be identified as production bottleneck. In cement, lime and pozzolan industry, the production limiting factor is usually related to the operation of exhaust fan. An example is false air inlet into the kiln or combustion chamber. The unwanted excess of air increases the air flow moved by the exhaust fan, but does not result in an increase in clinker production. The air temperature also has an impact in the exhaust fan efficiency. As it operates for a given volume, the correspondent mass of hot gases is lower. Therefore, a feasible measure to increase the mass of air that is transported by the fan is to cool down the gases by the end of the kiln. In whichever case, Dynamis performs a detailed study on the plant’s operational conditions to identify possible obstacles to higher productivity and, by the end, proposes solutions to increase the system’s efficiency.